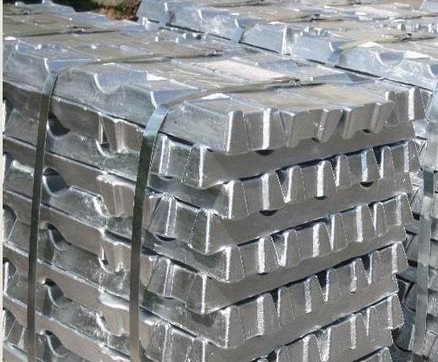
مشخصات شیمیایی مذاب روی
۲۲ام مرداد ۱۴۰۲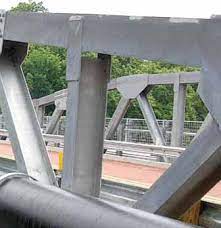
دوام زیاد گالوانیزه گرم
۱۵ام شهریور ۱۴۰۲بازیافت روی در گالوانیزه گرم ،فرایند گالوانیزه گرم، مانند هر فرایند صنعتی دیگر، ضایعات تولید می کند. با وجود اینکه تلاش های زیادی صورت گرفته تا میزان تولید ضایعات در حین فرایند به حداقل برسد، اما حذف کامل پسماندهای گالوانیزه امکان پذیر نیست. تولید ضایعات از مهم ترین عوامل مؤثر بر افزایش هزینه های فرایند، تخریب محیط زیست و کاهش منابع طبیعی فلزات در آینده نزدیک محسوب می شود.
این مشکلات، و بخصوص کمبود منابع طبیعی، محققان را بر آن داشته تا به تحقیق و توسعه تکنیک های جدید/بهبود یافته جهت استفاده مجدد ضایعات صنعتی به عنوان منابع ثانویه بپردازند. بعلاوه، پسماندهای صنعتی معمولاً در دسته مواد مضر و خطرناک قرار می گیرند و فرایندهای دفع/بازیابی خاصی باید برای آنها طراحی شود؛ در غیر این صورت، آسیب های بسیار جدی برای محیط زیست در بر خواهند داشت.
روش های بازیابی
بازیافت روی در گالوانیزه گرم،روش های بازیابی باید به گونه ای طراحی شوند که علاوه بر بازدهی بالا، زمان فراوری کوتاه، و هزینه های اولیه کم، به سادگی قابل اجرا بوده و از مواد و عملیات سازگار با محیط زیست استفاده کنند. در حالیکه بسیاری از انواع مواد زاید در حین فرایندهای تولید فولاد به روش های صنعتی قابل بازیابی هستند.
بازیابی پسماندهای فرایند گالوانیزه گرم، از جمله خاک، گرد و سرباره، به دلیل پیچیدگی مراحل بازایابی، کمتر در مقیاس صنعتی انجام شده و اغلب محصولات زاید گالوانیزه ترجیحاً دور ریخته می شوند.
در حین فرایند گالوانیزه گرم فولاد، واکنش میان آهن و روی سبب تشکیل سرباره در مذاب روی می شود که روی سطح مذاب انباشته شده و با نام خاک روی شناخته می شود و یا در وان مذاب ته نشین می گردد. روی موجود در این ضایعات گالوانیزه، اغلب به صورت ترکیبات بین فلزی آهن-روی یا ترکیبات غیر فلزی (عموماً اکسید روی) حضور دارد.
خاک روی که به صورت دستی از سطح مذاب جمع آوری می شود معمولاٌ حاوی ۷۰ تا ۹۶% روی فلزی اکسیدی است که ۱۲ تا ۱۵% کل روی مصرفی گالوانیزاسیون را به خود اختصاص می دهد. سرباره ته نشین شده نیز معمولاً حدود ۹۲ تا ۹۴% روی دارد. منبع دیگر روی ثانویه از محصولات گالوانیزه ای است که آسیب دیده یا از دور خارج شده اند.
گالوانیزه گرم، با توجه به امکان بازیابی ۱۰۰%، طول عمر بالای قطعات گالوانیزه شده، و کمترین اثرات نامطلوب بر محیط زیست، نقش قابل توجهی در راستای توسعه پایدار ایفا می کند. تکنیک های گوناگونی تاکنون به منظور بازیابی مؤثر ضایعات گالوانیزه مورد بررسی قرار گرفته اند.
بر طبق مطالعات اولیه، تنها با هم زدن مذاب روی حین گالوانیزه می توان حدود ۱۵% خاک روی را بازیابی نمود و افزودن خاک اره به مذاب، درصد بازیابی را به حدود ۵۵% افزایش می دهد. عملیات حرارتی خاک در دمای ۷۰۰oC می تواند ۵۰% روی فلزی را از خاک آن جدا کند . بهبود فرایندهای بازیابی روی، یک فاکتور کلیدی در افزایش بازدهی گالوانیزه گرم و کاهش هزینه ها محسوب می شود.
بازیافت روی در گالوانیزه گرم،فرایندهای بازیابی عموماً به دو دسته هیدرومتالورژیکی و پیرومتالورژیکی، یا ترکیبی از دو روش تقسیم می شوند. در فرایندهای هیدرومتالورژیکی معمولاً از جداسازی فلز با شستشوی اسیدی و ته نشینی انتخابی، تصفیه الکترولیزی، یا استحصال مایع-مایع استفاده می شود. هر چند که این تکنیک های بازیابی نتایج مطلوبی از خود نشان داده اند، اما اغلب آنها بسیار پیچیده و پرهزینه اند.
تکنیک های پیرومتالورژیکی نیز از عملیات حرارتی پسماندهای روی برای بازیابی فلز بهره می برند. خاک روی باید ابتدا به روش بال میل (آسیاب گلوله ای) و الک تحت عملیات قرار گیرد تا بخشی از اکسیدها از روی فلزی جدا شوند. سپس ضایعات الک شده مجدداً ذوب شده و به روی ثانویه تبدیل می شود. اکسیدهای بدست آمده نیز جهت تولید نمک های روی یا در فراوری روی از سنگ معدن آن (تولید روی اولیه) مورد استفاده قرار می گیرند.
چنانچه سرباره گالوانیزه حاوی درصد بالایی مس، نیکل و کبالت باشد می توان با ادغام دو فرایند پیرومتالورژیکی و هیدرومتالورژیکی آن را بازیابی نمود؛ به این ترتیب که ابتدا سرباره با سولفید آهن ترکیب شده و تحت یک عملیات حرارتی در محیط اکسید کننده قرار می گیرد. محصول این عملیات، اکسید آهن و دی اکسید گوگرد است. اتمسفر و دمای عملیات به گونه ای تنظیم می شود که عناصر فلزی مورد نظر، سولفات تشکیل دهند. سپس سولفات روی به عنوان ترکیب اصلی همراه با سولفات سایر فلزات مد نظر توسط یک فرایند هیدرومتالورژیکی، مانند شستشوی شیمیایی، احیا شده و فلزات مطلوب مورد استحصال قرار می گیرند. انرژی آزاد ترمودینامیکی سولفات روی ۰/۰۰۹MJ در ۸۰۰K است. مقایسه انرژی آزاد ترمودینامیکی سولفات روی با سولفات های سایر فلزات موجود در سیستم می تواند در تخمین میزان بازدهی فرایند بازیابی مفید واقع شود. بازدهی چنین فرایندی حدود ۴۹% گزارش شده است .
یک روش دیگر، که به عنوان جایگزین فرایندهای بازیابی مورد استفاده قرار می گیرد، استفاده مجدد ضایعات گالوانیزه گرم در سایر صنایع، از جمله تولید سیمان ، افزودنی به رنگدانه ها ، امولسیون آسفالت، و سرامیک ها است. هرچند که که این روش، راه حل مناسبی برای مدیریت ضایعات به نظر می رسد، اما توسعه یک فرایند ساده و مؤثر برای بازیابی روی از ضایعات می تواند نقش مهمی در کاهش هزینه های گالوانیزه و حفظ منابع طبیعی زمین ایفا کند.
گالوانیزه گرم سانتریفیوژ ،شرکت پارس پوشش با استفاده از تکنولوژی جدید سانتریفیوژ در بالای مذاب گامی موثر در پوشش دهی گالوانیزه گرم قطعات ریز و رزوه دار برداشته است. این تکنولوژی برای اولین بار توسط شرکت پارس پوشش در ایران اجرایی شده است.
شرکت پارس پوشش تولید کننده و تامین کننده انواع پیچ و مهره با پوشش های داکرومات و گالوانیزه اتصالات صنایع نفت، گاز و پتروشیمی،برق و …